Optimizing ESP Operations for a global leader in Upstream technologies

230+ Oil Wells
1 Goal: Customized, integrated, digitized workflows
In the complex world of ESP lifecycle management, our client faced a very common challenge: maximizing equipment utilization, minimizing inventory, and improving forecasting accuracy. Enter Optima's solution - the powerful Artificial Lift Lifecycle Management Module. With automated traceability and integrated functions, we ensured customized and complete workflows that meet all requirements.
Discovery
Snapshots



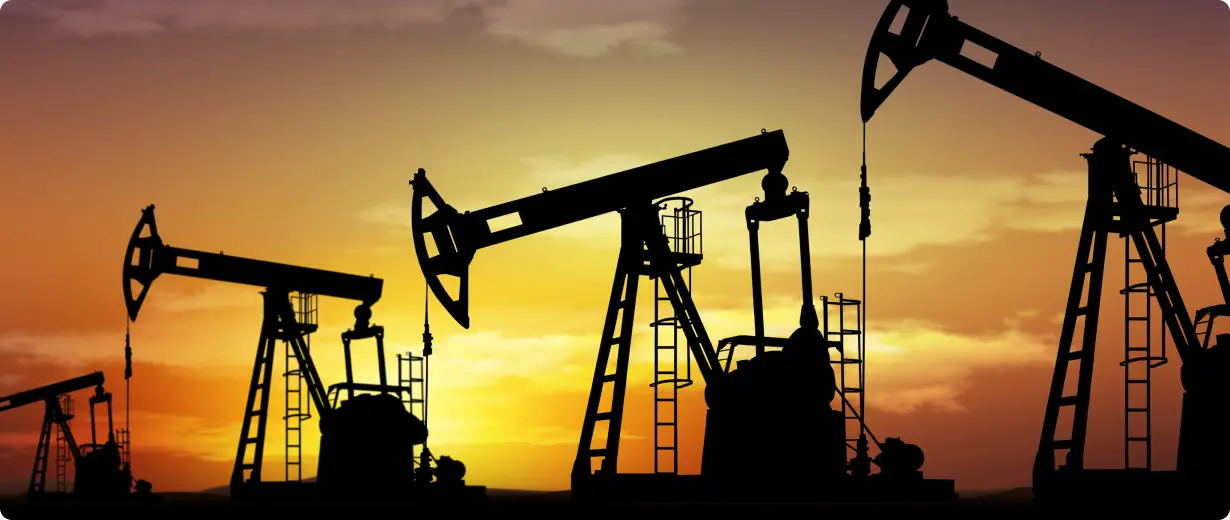
Key Challenges
To maximize the utilization of their equipment, minimize slow-moving inventory, and reduce lead time, which hinders the client’s operational efficiency and profitability.
The client is facing difficulties in accurately forecasting customer demand for their equipment, coordinating different functions within their organization, and integrating them into a unified platform for efficient planning.
The client is experiencing challenges in ensuring the traceability of their delivery workflow, automating workflow management processes, and obtaining real-time visibility into the progress of tasks and activities, leading to inefficiencies and potential delays.
Intriguingly woven since its inception in 2013, with over 230 Petroleum wells and an impressive portfolio of 40+ Invention Patents, our client harnesses its expertise, augmenting its prowess and forging global alliances with premier oilfield product and service providers from across the globe.
To address our client’s challenges, we developed the groundbreaking Artificial Lift Lifecycle Management Module. To begin with, our module offers a fully customized and integrated workflow that seamlessly tracks the entire lifecycle of a well, from the initial design of the equipment to its eventual replacement cycles. By incorporating automated traceability, we ensure that our clients have complete visibility and control over each stage of the process.
Inventory Management: For optimizing the inventory, we leverage advanced algorithms and data-driven analytics to minimize stock levels and optimize ordering points. By right-sizing inventory, our clients can achieve substantial cost savings while ensuring that they have the right equipment available when needed. Furthermore, our module allows for tailored technical specifications based on the unique characteristics of the field and wells. We empowered operators to optimize the ESP design and related operational parameters. This contributes to lower OPEX, as the systems operate at their peak efficiency.
Customized, collaborative Platform: Our integrated platform centralizes all relevant functions, enabling seamless collaboration between sales, engineering, manufacturing, planning, and operations. With automated traceability, integrated functions, and a focus on inventory optimization and tailored specifications, we have empowered our clients to maximize utilization, reduced inventory and lead time, improved forecasting accuracy, and ultimately achieved lower OPEX.

Business Benefits
- Reduced stock levels and ordering points, thus optimized inventory
- Maximum customization through tailored Field and Well operating modules
- Lower OPEX as design and optimized operational parameters